高速钢高温渗碳和低温淬火技术详解
930℃渗碳8h后,T1钢表面碳含量达到2.60%,碳含量高于1.0%的渗碳层深度约为0.75毫米。含大量碳化物形成元素的渗碳高速钢的化学反应机理不同于普通碳钢。在吸收和渗透过程中,它不仅以固溶体的形式存在于奥氏体中,而且以碳化物的形式存在,即碳化物在渗透的同时析出。
实际上,大部分渗碳在渗碳温度下以碳化物的形式析出,碳化物均为粒状,其类型随碳含量的增加按MC→M6C→M23C6→M3C的顺序变化。
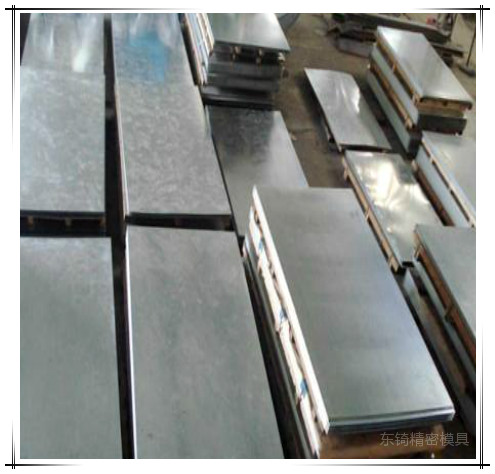
在上面的例子中,2%碳的渗透层已经含有大量的M3C碳化物。随着钢中碳含量的增加,固溶碳在一定奥氏体化温度下也略有增加。在一定范围内,固溶碳的增加有利于二次硬化,但过多会增加残余奥氏体量,降低二次硬度。
正如碳饱和影响高速钢的组织转变一样,渗碳层和芯层的淬火、回火和二次硬化特性是不同的。如果在渗碳和淬火之前在芯部加热到合适的温度,表面将过热并燃烧。
相反,如果目的是在正常淬火过程中发挥渗碳层的二次硬化性能,型芯将处于淬火欠热状态。当渗层表面碳含量过高,分布梯度过大时,上述矛盾更加突出,很难找到一个能基本发挥表层和芯层双重潜力的温度。
为了缓解这个矛盾。高速钢的渗碳一般分为两个阶段:渗透和扩散。炉气的碳势保持在低水平,但温度可以稍微升高。一般来说,这种钢的正常淬火温度的下限较低。例如,M2钢在1180~1150℃扩散后可以直接淬火。
正确选择渗碳温度、时间和炉气的碳势,经过渗碳、扩散、淬火和回火,可以获得高硬度、高耐磨性的表层和红硬度、高韧性的芯层,这是大多数模具和一些简单工具的外硬度和内韧性的良好配合。
可以看出,长期扩散处理和反复回火可以避免表面残余奥氏体过多,导致回火不充分和硬度低于芯。理想的表面硬度分布,高表面硬度和稳定的向内下降。全渗碳硬化层深度达到1毫米,66HRC以上深度为0.5毫米;经过低温淬火和普通回火后,铁芯的二次硬化温度为62~63℃。
制冷镦粗螺母的六角套筒模采用W6Mo5Cr4V2钢浸渗,1066℃固碳,开箱后空冷淬火,554℃×2.5h×2次回火,冷镦寿命达到240万件,是高速钢常规调质模的2.4倍,W18Cr4V钢模的6.8倍。